Você sabia que, de acordo com o IBGE, em média, 60% das empresas fecham após cinco anos de atuação, e o principal motivo é a falta de planejamento?
Se você é gestor de uma empresa ou está empreendendo, entenda como a metodologia MRP (Material Requirement Planning) pode ser uma importante ferramenta na hora de fazer a gestão de estoque de empresas varejistas e indústria. Confira abaixo.
Neste artigo você verá:
1. O que é MRP e quais seus benefícios
O planejamento de necessidades de materiais (MRP) é um sistema para calcular a quantidade de material e componentes necessários para fabricar um produto.
Basicamente, consiste em três etapas principais: fazer o inventário dos materiais e componentes disponíveis, identificar quais adicionais são necessários e, em seguida, programar sua produção ou compra.
O MRP, que é feito principalmente por meio de um software especializado, ajuda a garantir que o estoque certo esteja disponível para o processo de produção exatamente quando é necessário e com o menor custo possível.
Além disso, o MRP melhora a eficiência, flexibilidade e lucratividade das operações de manufatura. Implementar o MRP pode até mesmo tornar o time responsável pela produção mais produtivo, melhorar a qualidade do produto e minimizar os custos de material e mão de obra.
O planejamento também pode auxiliar os fabricantes a responder mais rapidamente ao aumento da demanda por seus produtos e evitar atrasos na produção e rupturas de estoque que podem resultar na perda de clientes. Manter o controle, por sua vez, contribui para o crescimento e estabilidade da receita.
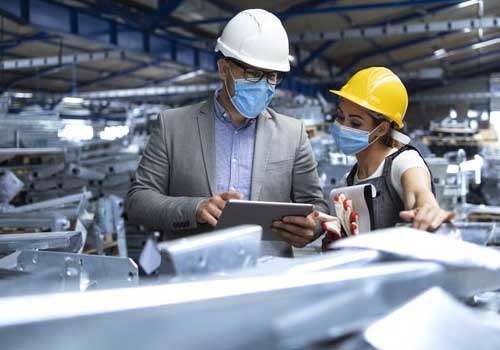
Acontece que o MRP é amplamente utilizado pelos fabricantes e, inevitavelmente, tem sido um dos principais facilitadores do crescimento e da ampla disponibilidade de bens de consumo acessíveis.
Sem uma maneira de automatizar os cálculos complexos e o gerenciamento de dados dos processos de MRP, é improvável que fabricantes individuais pudessem ter escalado as operações tão rapidamente quanto no meio século desde que o software MRP foi lançado.
O MRP surgiu nos Estados Unidos no fim dos anos 1960, como uma abordagem sistematizada voltada especificamente para a manufatura e, somente a partir da década de 1970, o MRP passou a ser sistematizado e informatizado, o que possibilitou realizar o cálculo das necessidades de materiais nas empresas de forma mais rápida e eficiente.
O objetivo principal do MRP é garantir que os materiais e componentes estejam disponíveis quando necessários no processo de produção e que a fabricação ocorra dentro do cronograma. Confira os principais benefícios MRP abaixo.
2. Como o MRP funciona?
Essencialmente, o MRP utiliza informações sobre a lista de materiais, dados de estoque e do cronograma mestre de produção para calcular os materiais necessários e quando eles serão necessários durante o processo de manufatura.
Essa lista de materiais é hierárquica e contempla todos os estágios da montagem de um produto e outros componentes necessários para fazer um produto, aliado à quantidade de cada item.
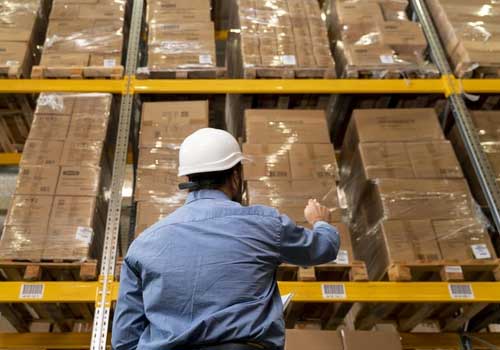
Os itens de estoque na lista são classificados como demanda independente ou demanda dependente. Um item de demanda independente é o produto acabado no topo da hierarquia.
Para organizar, os fabricantes determinam sua quantidade considerando os pedidos confirmados e examinando as condições de mercado, vendas anteriores e outros indicadores para criar uma previsão e, em seguida, decidir quanto é necessário fabricar para atender à demanda esperada.
Os itens envolvidos na demanda dependente, por outro lado, englobam a matéria-prima e os componentes necessários para fazer o produto acabado. Para cada um desses itens, a demanda depende de quanto material é preciso para fazer os componentes necessários de acordo com a hierarquia da lista de materiais.
Por ser um sistema de gerenciamento e controle de estoque para solicitar e rastrear os itens necessários para fazer um produto, o MRP deve ser essencial em qualquer operação. O tempo de processamento, período a partir do momento em que um pedido é feito e o item entregue, é outro conceito importantíssimo no MRP.
Existem muitos tipos de prazos de entrega. Os mais comuns são o prazo de entrega do material, o tempo que leva para solicitar materiais e recebê-los, e o prazo de entrega da fábrica ou da produção, ou seja, quanto tempo leva para fazer e enviar o produto depois que todos os materiais estiverem prontos.
2.1. MRP I e MRP II: entenda cada mais sobre eles
Você sabia que existem dois tipos de sistema MRP? O Manufacturing Resource Planning e o Material Requirements Planning.
O MRP I, ou seja, o Material Requirements Planning (Planejamento das Necessidades de Material) calcula o que deve ser produzido sem considerar a capacidade da fábrica. Entretanto, não faz a estimativa sobre a possibilidade de realizar a demanda.
Por outro lado, o MRP II, ou seja, Manufacturing Resource Planning (Planejamento dos Recursos de Produção), leva em conta a capacidade atual e suas estratégias de produção e possibilidades de acordo com os dados coletados sobre o processo.
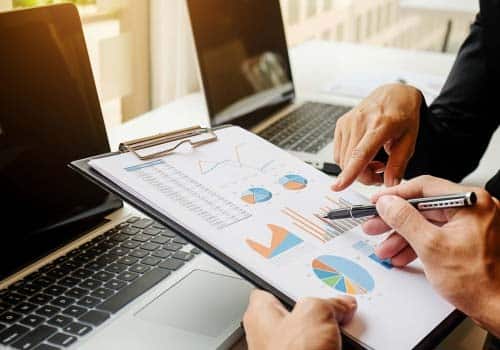
É importante saber que os dois tipos de MRP contemplam demandas de mercado em listas de materiais e ordens de produção.
Entretanto, apenas o MRP II conta com funções vinculadas como planejamento de vendas, negócios, operações, requisitos e capacidade de estoque.
Caso sua empresa opte pelo MRP II, problemas como a chegada da matéria-prima ao seu estoque até a entrega do produto acabado serão resolvidos.
Mas, se o investimento for muito alto no primeiro momento, ou se as suas necessidades de operacionalização de estoque e compras são mais simples, o melhor é escolher o MRP I.
Porém, como o crescimento da sua empresa é um objetivo a longo prazo, tenha em mente que o MRP I pode se tornar uma solução obsoleta com o tempo. O que faria com que a implementação do MRP II fosse necessária, fazendo-o gastar ainda mais.
Então, por este lado, a economia de curto prazo deve ser repensada para não significar gastos no futuro.
Embora os dois tipos de MRP sejam boas ferramentas para otimizar a gestão de estoque, contar com o cálculo automatizado de um serviço como o MRP II não deve ser a única medida a ser adotada para melhorar o processo da sua empresa. Estratégias como o Strategic Sourcing e o Supply Chain também devem ser analisadas para compor sua operação.
3. Como calcular o MRP
O plano mestre de produção pode ser feito baseado nos pedidos de venda, na programação de entrega recebida do cliente ou na previsão de vendas com base no histórico do período, mas isso vai depender da estratégia de cada negócio.
Entretanto, independente do tipo de indústrias todas precisam trabalhar com planos para produção, já que assim é possível ter uma visão geral do que deve ser produzido de produto finalizado, quando e qual a quantidade.
Após identificar a demanda, é hora de fazer a explosão da estrutura dos produtos acabados previstos na lista de materiais para saber as necessidades de fabricação e compra das matérias-primas e componentes fazem parte da estrutura de cada produto no plano mestre de produção.
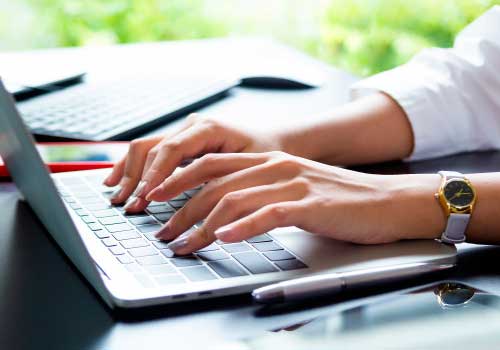
O sistema MRP identifica os itens que são dependentes, o que permite calcular a quantidade necessária de cada material, além de otimizar a compra ou produção de itens semelhantes que são usados em diversos produtos finalizados.
Ao observar o plano mestre de produção de um fichário escolar, o item gancho demora 3 dias (lead time) para ser feito, entretanto, depende do componente folhas de papel que demora cerca de 9 dias.
A partir desses dados, o MRP vai sugerir a data em que sua empresa deve fazer o Pedido de Compra de folhas de papel para atender a demanda e, por essa razão, é chamada de lógica de programação de trás pra frente.
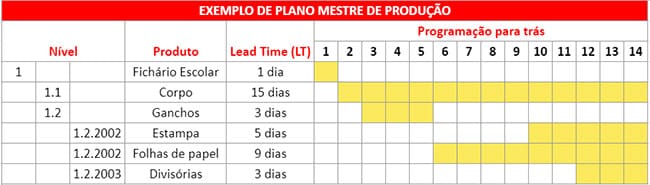
Após desmembrar o produto e construir a estrutura para a produção do mesmo e entender quais itens dependem de outros para serem feitos e qual o lead time de cada um, chegou a hora de conferir a prioridade e necessidade de cada material.
Este tipo de necessidade é conhecida como “Necessidade Líquida”, já que é o resultado da quantidade bruta que foi identificada na explosão da estrutura e sofreu com descontos sobre os itens que já estão disponíveis em estoque, pedidos de compra pendentes e as ordens de fabricação em andamento.
Portanto, um cálculo de MRP para apenas um dos itens da estrutura do produto finalizado em um mês seria assim:
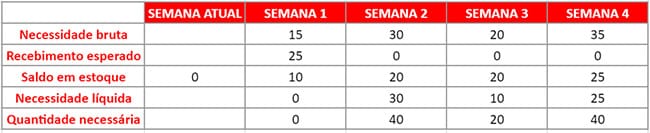
Para este cálculo, estipulamos uma demanda de 100 unidades, com lote mínimo de 10 unidades, estoque de segurança com cinco unidades e um período para produção de cerca de um mês.
Portanto, para calcular os materiais necessários para um produto finalizado é necessário realizar este processo para cada item da estrutura.
Porém, ao contar com um sistema, a tarefa de realizar esse cálculo manualmente faz-se desnecessária. Já para grandes empresas que contam com um alto número de produtos, o processo manual torna-se inviável, considerando que o cálculo é cheio de detalhes e está sujeito a erros durante o cruzamento de dados.
4. Como saber se o MRP é indicado para o meu negócio
A metodologia do MRP pode ser extremamente útil para todas as empresas com o objetivo de melhorar sua gestão do estoque, sem preocupações com relação aos cálculos, estimativa para demandas e gerenciamento e gestão de compras.
Certamente, em empresas cuja a operação seja grande e lida diariamente com um número alto de produção, o MRP é praticamente indispensável, visto que é um sistema que pode impactar o negócio de forma geral, cruzando informações e oferecendo resultados precisos.
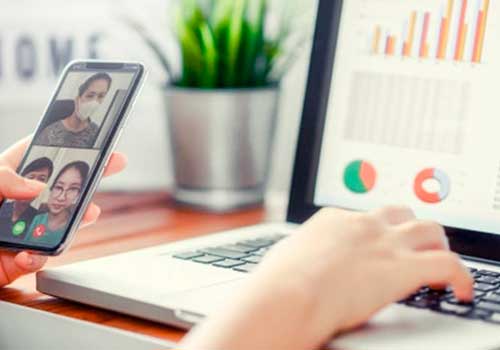
Esse é o caso das empresas que precisam estar em contato com inúmeros fornecedores diferentes de matéria-prima para o desenvolvimento de sua mercadoria.
Isso porque esse tipo de empreendimento costuma trabalhar com diferentes volumes de estoque com o objetivo de manter a produção sempre em um nível seguro, para “segurar as pontas” durante um contratempo sem parar a produção.
Vale lembrar que a utilização do MRP também é fortemente recomendada quando algum material ou componente sofre com instabilidades de fornecimento durante o período de produção da empresa.
No fim das contas, é um trabalho para o responsável pelo departamento de compras e fornecimento avaliar os prós e contras em implementar o MRP (seja o tipo I ou II) para a empresa.
Se a gestão de estoque é simples, não lidando com vários fornecedores, produtos e componentes para a produção dos itens comercializados, a implantação do sistema MRP não é a melhor escolha.
No entanto, é válido pensar a longo prazo no crescimento da empresa, além de questionar quanto tempo a empresa gasta com gestão de estoque nos dias de hoje.
No geral, a gestão do estoque nunca é uma tarefa simples, portanto, contar com estratégias e ferramentas que facilitem o processo e o auxiliem o time pode fazer toda a diferença no dia a dia.
Gostou das nossas dicas sobre o MRP? Viu só como ele também pode ser utilizado para quem importa, estabelecendo um processo muito mais organizado e uma gestão de estoque mais assertiva?
Então, fique ligado: para mais conteúdos como esse, inscreva-se e receba a newsletter semanal da Guelcos! Assim, você receberá os índices de fretes da China semanalmente, sempre às segundas-feiras.
